Exploring Lean and Six Sigma for Business Excellence
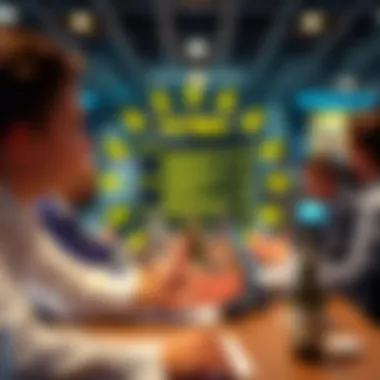
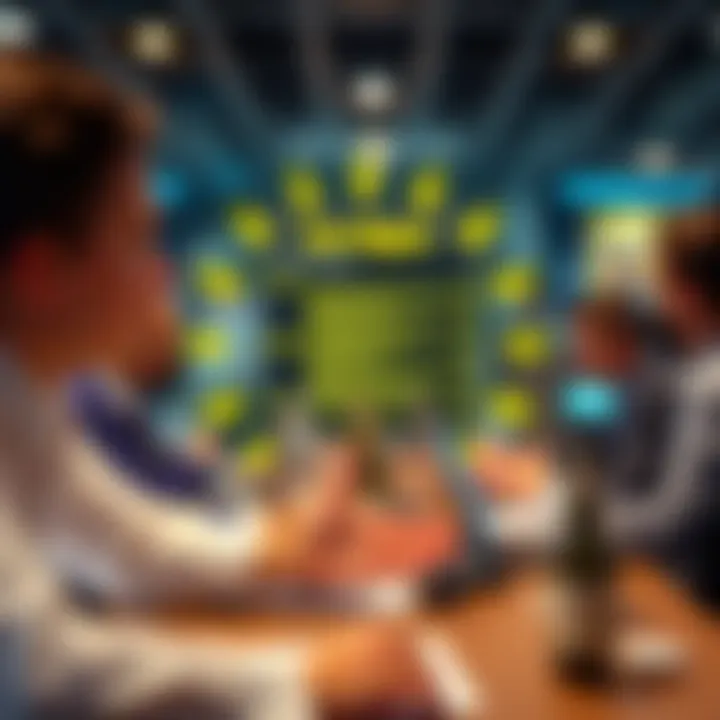
Intro
In today’s fast-paced business environment, operating efficiently is no longer an option; it's a necessity. As organizations strive to optimize processes and enhance productivity, two methodologies have emerged as leading contenders in the realm of operational excellence: Lean and Six Sigma. Both frameworks date back decades, each rooted in its own unique principles and philosophies, yet their combined strength offers companies a powerful toolkit to tackle waste reduction and variability improvement. This article serves as a guide to understanding these methodologies, their interconnectedness, and their practical applications in real-world settings.
Essential Definitions
To underpin our exploration, it is vital to clarify some essential terms. Lean focuses on eliminating waste from processes while maximizing value for the customer. This waste can take various forms, including overproduction, waiting times, and excess inventory. On the other hand, Six Sigma aims to minimize variability in processes, striving for near perfection by reducing defects to a rate of 3.4 per million opportunities. Together, they create a synergistic approach that not only enhances efficiency but also uplifts overall quality.
Lean Methodology
Lean revolves around the concept of value stream mapping, which visually represents every step of a process to identify non-value-adding activities. One of its central tenets includes continuous improvement or ‘Kaizen,’ a Japanese term meaning constant change for the better. Companies often adopt Lean principles to trim unnecessary steps, speed up delivery times, and create a culture that prioritizes customer value.
Six Sigma Methodology
Conversely, Six Sigma introduces a data-driven methodology that employs statistical tools to analyze processes and identify defects. Its acronym, DMAIC, stands for Define, Measure, Analyze, Improve, and Control, which outlines a structured approach to problem-solving. Six Sigma not only aims to improve quality but also emphasizes the importance of cultural transformation within organizations, empowering employees through training and knowledge.
Both Lean and Six Sigma create an ecosystem of continuous improvement, where employees feel valued and engaged in the process of refining their work environment.
Synergy of Lean and Six Sigma
When these methodologies are integrated, they form a robust framework that tackles operational challenges from two complementary angles. Lean identifies and removes waste, while Six Sigma focuses on reducing variability. This dynamic duo not only boosts efficiency but also enhances quality, leading to improved customer satisfaction and better financial performance.
The case studies highlighting this synergy are countless, spanning diverse industries from healthcare to manufacturing.
Concluding Thoughts
In summary, Lean and Six Sigma are not merely buzzwords in the business lexicon. They represent time-tested approaches that can significantly enhance operational performance. By examining their definitions, methodologies, and the synergy between them, this article aims to equip you with the knowledge needed to apply these strategies effectively in your organization. As we move forward, the next sections will delve deeper into their historical context and explore real-world applications, highlighting the transformational potential of these frameworks.
Preface to Lean and Six Sigma
The landscape of modern business is ever-changing, requiring organizations to adopt methodologies that not only enhance efficiency but also foster a culture of continuous improvement. Lean and Six Sigma have emerged as pivotal strategies in this regard, each presenting unique frameworks that, when integrated, can revolutionize operational processes.
Understanding Lean and Six Sigma is essential for business leaders who aim to streamline operations and enhance quality. Lean focuses primarily on minimizing waste and maximizing value for the customer. This technique directly affects the bottom line, as reducing waste can lead to substantial cost savings. Through this lens, businesses can offer more competitive pricing or improve profit margins, allowing them to stay ahead in a saturated market.
Conversely, Six Sigma takes a detailed approach to quality management by using statistical tools and methodologies to reduce defects. The emphasis here is on precision and consistency; these attributes are critical, especially in industries where zero defects can be the difference between success and failure. When we talk about high-quality outputs, Six Sigma's insights are invaluable, ensuring that organizations meet customer expectations consistently.
The ongoing relevance of these methodologies cannot be overstated. Businesses operating in today's fast-paced environment must not only adapt but also evolve. The integration of Lean and Six Sigma offers a robust solution, allowing firms to achieve excellence in both process efficiency and quality control. This article aims to delve deeper into these strategies, exploring their definitions, historical context, core principles, and the practical implications of their integration.
Both Lean and Six Sigma serve as guiding principles for businesses, enabling them to navigate through complexity and achieve operational excellence efficiently.
By examining the synergies between Lean and Six Sigma, this analysis sheds light on how businesses can foster a culture of improvement that stretches beyond traditional operational goals. It reveals how adopting these methodologies can lead organizations to create more value for their customers while simultaneously enhancing their internal processes.
Core Principles of Lean
Lean methodology is akin to a fine-tuned machine; every gear in its complex structure serves a distinct purpose. The core principles of Lean focus on enhancing operational efficiency, streamlining processes, and creating value for customers while minimizing waste. Exploring these principles is critical, as they serve as the bedrock upon which successful Lean implementations rest. Companies adopting lean practices often witness improvements in productivity and overall customer satisfaction, ultimately leading to increased profitability.
Value Stream Mapping
Value Stream Mapping (VSM) is a powerful tool used within Lean methodology that helps organizations visualize their processes from start to finish. By sketching out the step-by-step flow of materials and information, businesses can identify bottlenecks and areas where waste occurs.
Through VSM, a firm can appraise both the value-added and non-value-added activities. One notable benefit of this is that it empowers teams to prioritize improvements. For instance, a manufacturing unit may discover that its quality checks, while essential, are consuming an excessive amount of time due to redundancies. By addressing these redundancies, Lean practitioners can shave off seconds or minutes that contribute to greater operational efficiency. It's not just a map; it's a roadmap to success.
Eliminating Waste
Eliminating waste, known in Lean circles as "Muda," is at the heart of Lean philosophy. Waste manifests in various forms, from excess inventory to unnecessary motion or overproducing beyond customer demand. Recognizing these forms is crucial to streamline operations.
- Overproduction: Manufacturing more than what is needed, leading to excess inventory.
- Waiting: Time lost when processes or people are idle, costing time and money.
- Transportation: Unnecessary movement of materials or products that adds no value.
- Extra Processing: Performing more work than required to meet customer needs.
- Defects: Errors that require correction, which not only wastes materials but also time and resources.
By systematically identifying and eradicating these wastes, businesses can direct their resources towards areas that enhance value for customers. For example, a grocery store may decide to optimize its checkout process to reduce waiting time, directly influencing customer satisfaction.
Continuous Improvement (Kaizen)
Continuous Improvement, commonly referred to by its Japanese word "Kaizen," embodies a core ethos of Lean thinking. It's not a one-time fix but a consistent effort to make small, incremental changes that collectively lead to significant improvement over time. Kaizen focuses on empowering employees at all levels to look for ways to enhance processes and eliminate inefficiencies.
For instance, a healthcare provider might establish a Kaizen event where staff members brainstorm ways to reduce patient wait times. In this collaborative setting, everyone has a voice, and their insights may lead to actionable strategies, such as revising scheduling protocols or streamlining patient intake procedures.
In summary, the core principles of Lean, including Value Stream Mapping, waste elimination, and the philosophy of Continuous Improvement, collectively shape a framework that drives businesses toward operational excellence. As organizations delve deeper into these principles, they not only enhance productivity and service delivery but also foster a culture of sustained improvement and adaptability.
"Lean is about improving processes and equipping everyone in the organization with the mindset and tools to make those improvements."
Core Principles of Six Sigma
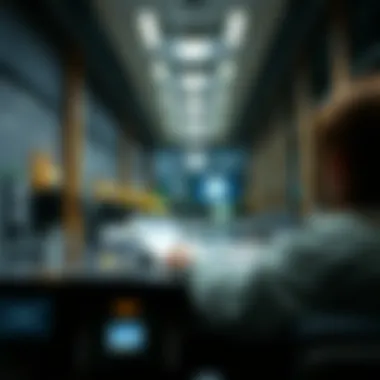
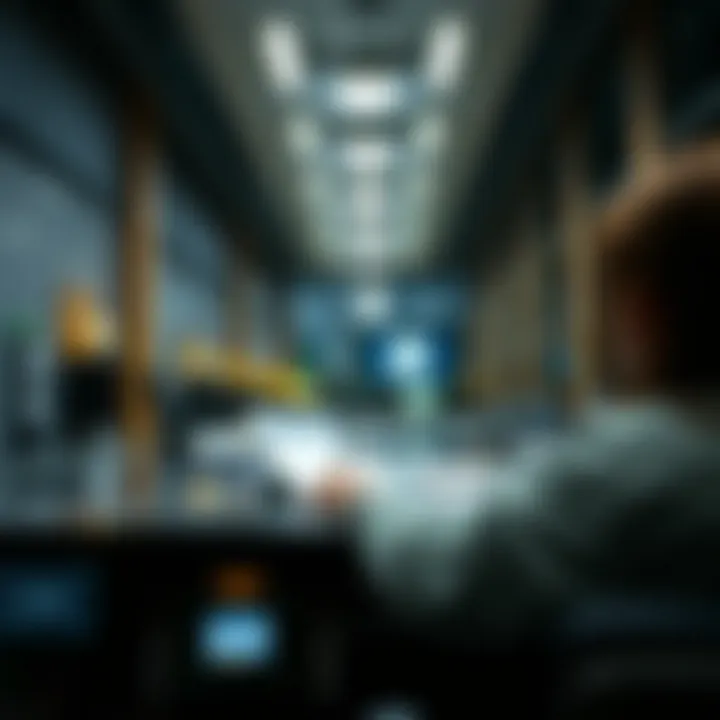
Six Sigma represents a set of powerful tools and techniques aimed at improving processes and reducing variation within them. Its core principles framework allows businesses to become more efficient and minimize errors, driving operational excellence. By aligning with the needs of customers and leveraging data, organizations can expect significantly enhanced quality and productivity. Understanding these principles is crucial as it helps in navigating a competitive landscape where precision often beats speed.
DMAIC Methodology
At the heart of Six Sigma lies the DMAIC methodology: Define, Measure, Analyze, Improve, and Control. Each phase serves a clear purpose and builds upon the preceding one, leading teams through a structured approach to problem-solving.
- Define: This stage outlines the problem to be addressed and identifies the project goals. Teams must clearly articulate what success looks like. A precise definition often sets the tone for the entire project.
- Measure: Data collection is key here. The objective is to gather relevant information about current processes to establish baselines. Real-life measurements guide future decisions.
- Analyze: This phase digs into the collected data to uncover root causes of defects or inefficiencies. Tools such as fishbone diagrams or Pareto charts may aid in visualizing problems clearly.
- Improve: Solutions to address identified issues are developed. Teams often brainstorm creative, impactful strategies tailored to existing constraints. Testing solutions before wide-scale implementation helps mitigate risks.
- Control: To sustain improvements, control plans are put in place. This includes setting standards, ongoing monitoring, and regular process audits.
The DMAIC methodology is fundamental for project success, ensuring a systematic approach that yields tangible results.
Defect Reduction
Defect reduction is a core aim of Six Sigma, which strives to achieve a level of quality that results in fewer than 3.4 defects per million opportunities. The concept fundamentally shifts perspectives on quality assurance. Instead of only inspecting final products for defects, Six Sigma promotes finding and eliminating defects throughout the entire process.
Some critical elements in this realm include:
- Identifying Variability: Understanding what causes variability—be it human error, machine malfunction, or inadequate processes—is essential. Once identified, teams can focus on these sources to minimize errors.
- Process Standardization: Establishing protocols helps ensure tasks are performed consistently. When everyone is on the same page, the risk of defects diminishes.
- Engagement of Employees: When team members feel involved in defect reduction efforts, there is buy-in. Such involvement cultivates a culture that prioritizes quality.
Through a focus on defect reduction, organizations reduce costs, enhance customer satisfaction, and improve overall competitiveness.
Statistical Tools and Techniques
Statistics play a vital role in Six Sigma as they provide the empirical foundation for decision-making. Several tools and techniques enhance project performance, resulting in data-driven strategies. Some of these include:
- Control Charts: Control charts allow you to visualize process variability over time, pinpointing trends or shifts while providing a visual framework to monitor performance.
- Process Capability Analysis: This technique evaluates how well a process meets specifications. Knowing the capability indices helps organizations assess where improvements are necessary.
- Hypothesis Testing: A useful statistical approach for comparing different groups to determine if one approach leads to better results than another.
Ensuring effective utilization of statistical tools bolsters the integrity of any Six Sigma initiative. It creates a measurable path toward improved operations and diminished waste.
In summary, the core principles of Six Sigma—especially the DMAIC methodology, defect reduction, and the use of statistical tools—create a clear pathway for organizations that aspire to elevate their performance levels. By embedding these principles into an organization's fabric, an environment that supports continuous improvement and excellence is forged.
The Synergy Between Lean and Six Sigma
The integration of Lean and Six Sigma has gained traction in various industries as it combines the strengths of both methodologies. The marriage of these two has proven to be beneficial in enhancing operational efficiency and overall performance. When organizations embrace this synergy, they tap into a framework that not only focuses on reducing waste and improving quality but also emphasizes the crucial value of continuous improvement.
Companies have realized that using Lean's efficient principles alongside Six Sigma’s focus on quality can create a more streamlined approach to process improvement. This combined strategy leads to more efficient use of resources, a decreased time to market for products, and higher customer satisfaction rates.
In essence, this synergy ensures that organizations not only produce high-quality outputs but also effectively manage their processes to prevent waste. Here are some specifics on how Lean and Six Sigma complement each other effectively:
Complementary Strategies
Lean prioritizes the elimination of waste in every step of the process. This focus means that efficiency is maximized while the value delivered to the customer is increased. On the other hand, Six Sigma emphasizes reducing variability and defects, ensuring that processes maintain consistent quality.
Thus, when these strategies are applied together, organizations can:
- Address and streamline processes (Lean)
- Reduce defects and enhance quality control (Six Sigma)
- Foster a culture of continuous feedback and improvement (both methodologies)
These approaches do not just coexist; they enhance one another. Lean can identify areas needing improvement, while Six Sigma can provide the quantitative analysis required to measure improvements achieved.
Integrated Frameworks
Organizations seeking to implement a blended approach generally develop an integrated framework that combines Lean and Six Sigma principles. A key aspect of this integrated framework is DMAIC (Define, Measure, Analyze, Improve, Control), a Six Sigma tool that can be complemented with Lean principles such as Value Stream Mapping or 5S.
This integration allows organizations to:
- Clearly define projects and expectations using Lean concepts
- Measure process performance incorporating Six Sigma metrics
- Analyze critical processes to identify root causes of inefficiencies
- Implement targeted improvements based on qualitative Lean insights while ensuring they align with Six Sigma quality parameters
- Control processes post-implementation to sustain improvements
The blended framework can be visualized as a continuous loop that facilitates lasting change rather than a one-time effort to fix problems.
Case Studies of Integration Success
Real-world applications of Lean and Six Sigma integration illustrate the profound impact of this synergy. For example, the Toyota Production System, often heralded as the epitome of Lean, also incorporates aspects of Six Sigma. By leveraging both methodologies, Toyota has achieved a reputation for exceptional quality and efficiency.
Similarly, companies like GE and Motorola have adopted this approach to improve their product development cycles and customer satisfaction rates. GE, through a structured Six Sigma attitude paired with Lean’s waste removal strategies, managed to reduce cycle times significantly, achieving impressive results that resonate with their company values.
These case studies are not merely success stories; they serve as proof that Lean and Six Sigma, through a unified lens, can help businesses thrive in the competitive landscape. This framework is not just a theory; it's a practice that yields real, transformative results.
Implementation Challenges
Implementing Lean and Six Sigma in an organization is not all smooth sailing. There are often bumps along the road that can hinder progress and dampen the enthusiasm of those involved. Therefore, understanding these implementation challenges is crucial. It allows organizations to anticipate roadblocks, adopt proactive strategies, and ultimately achieve the desired transformation in their business processes. Embracing Lean and Six Sigma is like planting a seed: the right care is required to ensure it grows. Each challenge presents an opportunity for refinement and enhances the chances of successful implementation.
Cultural Resistance
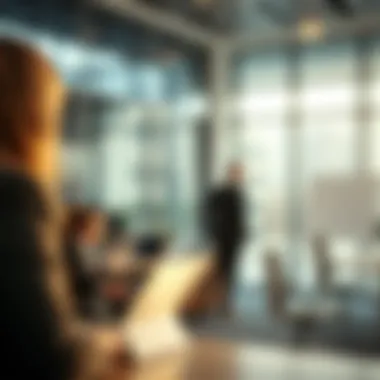
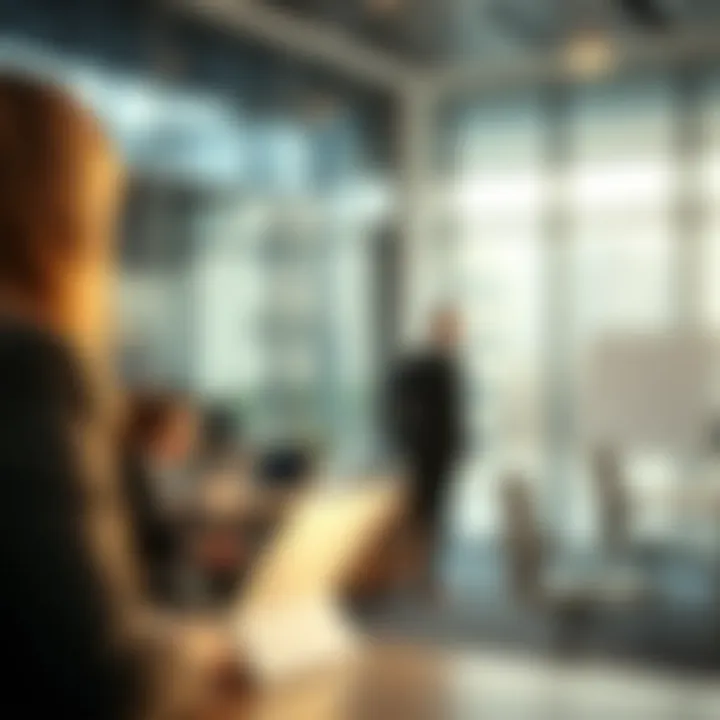
Cultural resistance is a major hurdle in the path of Lean and Six Sigma adoption. It’s common for employees to cling onto traditional ways of working, even if they are inefficient. The fear of change can be powerful. Employees might worry about job security, question the motives behind shifting practices, or simply feel skeptical about the new methods. This is where strong leadership comes into play. Leaders should cultivate a culture that embraces change rather than fears it. They might begin by engaging staff in conversations about the benefits of Lean and Six Sigma, creating an environment where feedback is welcomed and actively sought.
For instance, companies that have actively involved employees in the decision-making process around these methodologies often report increased buy-in. By demonstrating how Lean and Six Sigma can simplify their workload rather than burden them, organizations can turn doubters into advocates.
Resource Allocation
Another significant factor that affects successful implementation is resource allocation. Organizations often underestimate the resources needed for effective Lean and Six Sigma practices. It’s not just about money; human resources, time, and technology are equally critical. Organizations must allocate time for training, ensure that teams are adequately staffed, and invest in tools that facilitate these methodologies.
Consider this: a company that assigns one person to spearhead a Lean initiative without additional support runs the risk of burnout and disillusionment. Instead, it's wise to form cross-functional teams dedicated to driving these projects. This enables diverse perspectives and encourages collaboration.
Moreover, aligning resources with organizational goals is key. Companies that provide clear, well-defined objectives often find that their teams are more motivated and engaged in the implementation process.
Training and Skill Development
Training and skill development are imperative for the successful introduction of Lean and Six Sigma practices. Without proper training, efforts may fall flat, as employees might lack the understanding necessary to apply these methodologies effectively. Simply put, knowledge is power. Offering comprehensive training will not only equip employees with essential skills but also foster a sense of ownership in the processes they are a part of.
Training can take on various forms. Online courses, on-site workshops, or mentorship from experienced practitioners are all effective strategies. The emphasis should be placed on creating a fluid learning environment that encourages continuous improvement. Using real-world scenarios during training aids in bridging theory to practice. When employees can envision how Lean and Six Sigma apply within their specific context, they are more likely to embrace these changes.
Tools and Techniques for Lean and Six Sigma
In the landscape of business operations, the sophistication of tools and techniques designed for Lean and Six Sigma is paramount. These methodologies emphasize the importance of systematic approaches that not only drive efficiency but also elevate the overall customer experience. By integrating these tools into their core practices, organizations can ensure they are harnessing the full potential of their processes, resulting in more effective output and enhanced competitiveness.
Value Stream Analysis
Value Stream Analysis (VSA) acts as a pivotal methodology in identifying and controlling the flow of materials and information through a business process. Quite simply, it allows organizations to visualize their workflows, pinpointing areas that need improvement with laser focus.
- Importance: VSA is crucial because it identifies waste—unproductive activities that do not add value from the customer’s perspective. Without such clarity, inefficiencies can linger, adversely affecting overall productivity and profitability.
- Benefits: By applying VSA, businesses can streamline operations, reduce cycle times, and allocate resources more effectively.
- Considerations: It's essential to approach VSA with a fresh pair of eyes, avoiding the pitfalls of habitual thinking. Regular reviews can better align processes with evolving customer expectations.
In practice, VSA can be utilized through mapping exercises that make use of simple diagrams to visualize workflows. By integrating this with other Lean tools, like the 5S methodology, organizations can establish a robust framework for continuous assessment and improvement.
Control Charts
Control Charts are a powerful statistical tool used within the Six Sigma framework to monitor process stability over time. They provide a visual representation of variation in processes, helping organizations determine if their operations are in control or if corrective actions are needed.
- Importance: Understanding process variation is fundamental. Control charts help distinguish between common cause variations, which are inherent to the process, and special cause variations that arise from external factors.
- Benefits: By employing Control Charts, businesses can reduce process variability, strengthening their quality assurance practices and enhancing product consistency.
- Considerations: Effective use of Control Charts requires accurate data collection. Organizations must train teams on data integrity and statistical interpretation to make informed decisions.
Implementing Control Charts as a regular part of performance evaluation fosters a culture of data-driven decision making. This trend can lead to better forecasting and improved operational strategies.
Root Cause Analysis
Root Cause Analysis (RCA) is an essential technique that digs deep beneath the surface of problems to uncover the underlying causes of defects or inefficiencies. This method goes beyond symptom management, directing focus on resolving issues efficiently at their source.
- Importance: Knowing the root cause is critical. If organizations only address the symptoms, they risk recurrent issues that can undermine operational effectiveness.
- Benefits: RCA promotes long-term solutions, which can dramatically reduce costs associated with defect correction and customer dissatisfaction.
- Considerations: Effective RCA requires a systematic approach. Techniques like the "5 Whys" or Fishbone Diagrams can facilitate identification of root causes, but it’s necessary to foster an open and honest workplace culture where employees feel free to discuss errors.
"The journey of a thousand miles begins with one step." - Lao Tzu. In the world of Lean and Six Sigma, each step, rooted in the right tools, can lead to transformative results.
To summarize, by utilizing sophisticated tools like Value Stream Analysis, Control Charts, and Root Cause Analysis, organizations can significantly enhance their operational efficiency. These techniques help identify waste, stabilize processes, and get to the heart of problems, ultimately leading to a culture characterized by sustainable improvement.
Measuring Success
In the realm of Lean and Six Sigma, measuring success is not just a formality; it’s the bedrock upon which sustainable improvements are built. Without clear metrics, organizations can easily find themselves adrift, unsure of whether their efforts are yielding tangible results or merely running in circles. By establishing a system for measurement, businesses can continually assess their progress, adapt strategies accordingly, and cement their commitment to a culture of continuous improvement.
The advantages of having well-defined success measurement criteria include enhanced accountability and informed decision-making. Here’s why it holds monumental significance:
- Clarity: Establishes clear expectations and allows for aligned objectives across teams.
- Benchmarking: Helps in comparing current performance against industry standards or historical data.
- Feedback Mechanism: Offers real-time insights into what works and what doesn’t, enabling prompt adjustments.
“What gets measured gets managed.” – Peter Drucker
This simple yet profound statement underscores the importance of effective measurement in any business initiative.
Key Performance Indicators (KPIs)
Key Performance Indicators, or KPIs, serve as the guiding stars for organizations implementing Lean and Six Sigma methodologies. These defined metrics not only gauge progress but also illuminate areas requiring further efforts or attention.
Common KPIs in Lean and Six Sigma often involve:
- Cycle Time: Measures the time taken to complete a process from start to finish. A reduction in cycle time often signals improved efficiency.
- First Pass Yield (FPY): Indicates the percentage of products manufactured correctly without the need for rework. A higher FPY means fewer defects.
- Cost of Poor Quality (COPQ): Calculates the costs associated with failures, defects, and poor performance. Lower COPQ typically signifies better quality management.
The strategic selection of KPIs directly influences an organization’s ability to achieve Lean and Six Sigma goals. Businesses need to be selective and ensure these KPIs align with their overarching objectives to effectively monitor performance and foster a proactive approach toward improvements.
Return on Investment (ROI)
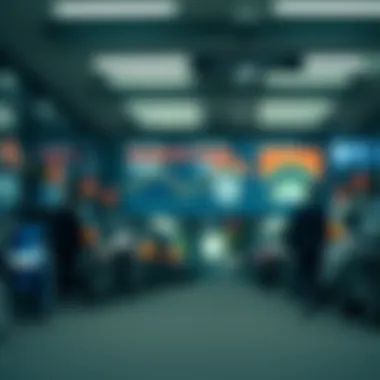
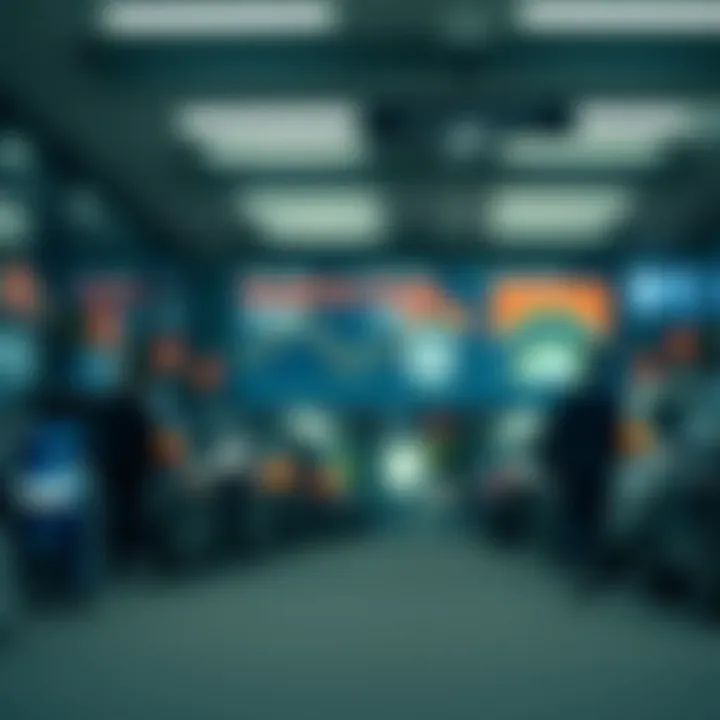
In the high-stakes world of business, understanding the return on investment (ROI) aspect of Lean and Six Sigma efforts is crucial. It’s not merely about slashing costs or improving processes; it’s about gauging the financial impact and benefits realized from those improvements.
The calculation of ROI in Lean and Six Sigma involves assessing:
- Initial Costs: Costs associated with implementation, including training, tools, and personnel.
- Savings Calculated: Financial benefits realized through waste reduction, increased sales, and better quality outcomes.
- Net Gain: The difference between savings and costs which exemplifies the overall health of the investment.
To genuinely appreciate ROI, organizations should look beyond the immediate financial returns and consider long-term benefits like enhanced customer loyalty and market competitiveness. A savvy business understands that the fuller picture matters.
Customer Satisfaction Metrics
At the center of Lean and Six Sigma strategies lies the truth that customer satisfaction is king. It’s vital to measure how effectively these methodologies enhance the customer experience. After all, a happy customer often translates to repeat business and referrals.
Key metrics to track customer satisfaction include:
- Net Promoter Score (NPS): Measures customer loyalty by asking how likely they are to recommend a company to a friend or colleague.
- Customer Satisfaction Score (CSAT): Collects direct feedback from customers about their satisfaction with specific transactions or interactions.
- Customer Effort Score (CES): Assesses how easy it is for customers to interact or resolve issues with the business.
Monitoring these metrics is paramount to understanding those nuanced shifts in customer sentiments and preferences. Ultimately, a focus on customer satisfaction ensures that Lean and Six Sigma efforts genuinely deliver value, cementing the loyalty and trust vital for long-term success.
Future Trends in Lean and Six Sigma
The landscape of Lean and Six Sigma is changing, driven primarily by advances in technology and shifts in consumer expectations. Understanding these trends is vital for organizations aiming to stay ahead in the competitive game. By integrating modern practices into Lean and Six Sigma frameworks, companies can not only enhance their efficiency but also ensure their relevance in a world increasingly dominated by digital transformation, data analytics, and sustainability. Each trend brings its own unique challenges and opportunities, making it essential for business leaders to embrace these changes thoughtfully.
Digital Transformation
Digital transformation is no longer a buzzword; it’s a necessity for any business wishing to thrive. Lean and Six Sigma methodologies must adapt to include digital tools that streamline processes and enhance operational efficiency. With the rise of cloud computing, companies can now access real-time data, enabling quicker decision-making processes that are central to Lean and Six Sigma philosophies.
For instance, utilizing technology for value stream mapping can provide immediate insights into workflow inefficiencies. Instead of relying only on traditional methods, businesses can use software solutions that allow for dynamic reporting and immediate adjustments. This fosters agility, a characteristic of Lean practices.
- Benefits of Digital Transformation in Lean and Six Sigma:
- Real-time data access supports faster decisions.
- Automated reporting reduces manual labor and errors.
- Enhanced collaboration tools lead to better communication among teams.
Adopting digital solutions might seem demanding at first glance, but the operational benefits can yield productive results and substantial cost savings over time. A significant portion of companies that have embraced digital transformation report improved productivity and a drastic decrease in cycles needed for tasks.
Artificial Intelligence and Data Analytics
Artificial Intelligence (AI) is reshaping the way organizations collect and analyze data, providing deeper insights that are crucial for continuous improvement. The marriage of AI with Lean and Six Sigma methodologies facilitates more precise identification of root causes of problems through enhanced analytics.
AI algorithms can analyze vast data sets at speeds which humans can't match, flagging trends and anomalies that might otherwise go unnoticed. For instance, machine learning can help in predictive maintenance, reducing the likelihood of machine failures and ensuring smoother operations.
- Considerations for Utilizing AI in Lean and Six Sigma:
- Understand the data: Organizations must have a solid grasp of what data they have and how it can be used.
- Invest in training: Staff should be trained on both Lean/Six Sigma principles and the tools used in AI.
- Start small: It's advisable to pilot AI projects in small segments before scaling across the organization.
With these technologies in play, companies can enhance their efforts to reduce defects and improve quality, which is foundational to Six Sigma.
Sustainability Initiatives
In an era where environmental concerns take center stage, integrating Lean and Six Sigma practices with sustainability initiatives becomes paramount. Organizations are increasingly expected to be responsible stewards of resources, and Lean's hallmark of waste reduction aligns perfectly with sustainability goals.
Adopting sustainable practices not only demonstrates social responsibility but also offers operational efficiencies. By minimizing waste, businesses can see a decrease in material costs, which can directly translate to greater profitability. Moreover, a growing number of consumers prefer companies that are environmentally conscious, impacting buying decisions.
- Ways to Embrace Sustainability in Lean and Six Sigma:
- Conduct energy audits: Identifying areas of energy consumption can yield insights for reducing waste.
- Implement green supply chain practices: Work with suppliers who prioritize eco-friendly processes.
- Encourage a culture of sustainability: Engage employees in sustainability initiatives to make it a core value of the organization.
A strong sustainability initiative can act as a differentiator in the marketplace, attracting customers and investors alike.
"To navigate the future successfully, companies must not only adapt but innovate within the frameworks of Lean and Six Sigma, ensuring that their processes are both efficient and sustainable."
In summary, the future of Lean and Six Sigma lies in understanding and integrating digital transformation, AI, and sustainability initiatives. Organizations willing to embrace these trends will likely see significant improvements in both their operational and financial performance.
Culmination
In closing, it’s essential to recognize the profound impact that Lean and Six Sigma methodologies have on today's business landscape. Their strategic importance cannot be understated, particularly in an era defined by rapid change and heightened competition. Organizations that choose to adopt these frameworks are not merely opting for better processes, they are committing to a philosophy of continuous evolution. This commitment leads to enriched customer experiences, greater employee engagement, and ultimately, robust financial performance.
Strategic Importance
The strategic importance of Lean and Six Sigma lies in their ability to deliver tangible value through streamlined operations and waste reduction. By focusing on improving efficiency and quality, companies can respond agilely to market demands, ensuring that they remain relevant in an evolving economy. In particular, this convergence of methodologies supports:
- Cost Savings: Reduced waste means lower operational costs, allowing for better pricing strategies and increased margins.
- Enhanced Quality: By applying statistical tools, firms can minimize defects in their services and products, ultimately boosting customer satisfaction.
- Cultural Shift: Embracing these methodologies fosters a culture of innovation and teamwork, where employees at all levels are encouraged to contribute to continual performance improvements.
As Lean and Six Sigma become foundational approaches within an organization's strategy, the potential for competitive edge expands. Companies operating without these frameworks risk stagnation, as they may fall behind more adaptive competitors.
Call to Action for Businesses
For organizations ready to harness the power of Lean and Six Sigma, the next steps are crucial. Business leaders should:
- Conduct a Gap Analysis: Assess current processes to identify areas ripe for improvement.
- Invest in Training and Development: Equip your team with the necessary skills. Consider certified training programs or workshops through reputable institutions like the American Society for Quality ASQ.
- Engage Stakeholders: Involve team members from all departments in brainstorming and problem-solving sessions. A well-rounded perspective often unveils insights that top-down approaches might miss.
- Set Measurable Goals: Define clear KPIs to track progress in implementation and ensure alignment with strategic objectives.
- Communicate Successes: Highlight early wins to build momentum. Sharing success stories within the organization can increase buy-in and motivation.